Find out more about shells and Mother of Pearl (“MOP”) by the Duke of Pearl – the world’s best source for top quality mother-of-pearl (“MOP”) and abalone shell materials and co-inventors of ABALAM (since 1967).
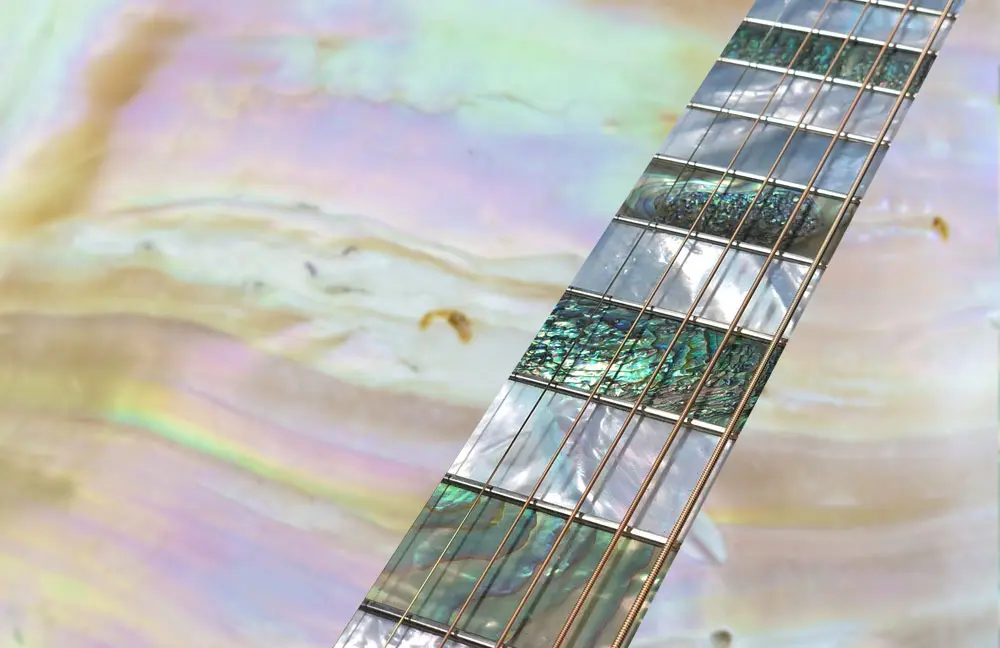
THE HISTORY OF NACREOUS SHELLS
Shells and Mother of Pearl – Knowledge Base
Can you give a brief history of the nacreous shell fisheries?
Ocean pearl oyster fisheries have always primarily been about getting pearls (or animals to grow cultured pearls in), with meat as a secondary market, and the shells as a byproduct. There are records of commercial pearling as far back as 2000 B.C., and up until the early 1900’s the only way to recover oysters or abalone was by free diving using no air supply or equipment other than a rope to the diver, maybe an animal horn nose clip, and a gathering basket held in one hand. Typically it was desperate work, often forced labor, with a diver receiving scant wages and only a very few if any of the animals brought up.
The Japanese diving industry was originally about the giant “nacre d ‘orient” or “Goldfish” Awabi Abalone (so often used in antique folding hand fans) and the divers were all young girls to middle aged women known as “ama”. They wore nothing but small goggles and a loincloth, and could go as deep as 60 feet in shark and octopus infested waters. After the early 1900’s introduction of cultured pearls, the ama found use for their skills at the quickly expanding Akoya Oyster farms (we sell this material, but call it “Agoya” since that’s how the Koreans introduced it to me decades ago, and it’s too much trouble to switch now to the correct name!).
India and Sri Lanka, the Persian Gulf, and the Red Sea were the traditional pearl oyster fisheries using free divers. But huge pearl-fishing steamships were introduced in 1904 carrying heavy equipment and up to 100 divers. This new technology involved toothed dredges that were raked over the oyster beds, which triggered the animal’s open valves to snap shut on the teeth, which were then hauled to the surface and harvested. The divers recovered any remaining animals using heavy diving bells connected to an air supply. These methods quickly exhausted the shell populations.
In Australia, the aborigines never placed any special value on oysters other than as food. But when Europeans arrived in 1861, the natives were conscripted as free divers to work the 3,000 mile long oyster banks between Freemantle and Cooktown, and the Torres Strait and Great Barrier Reef beds. By the early 20th century all these pearl beds had been reduced to almost nothing. Modern fisheries employ hard-hat diving suits with supplied air.
With their invention in 1893 and the subsequent early 1900's introduction of cultured pearls from commercially farmed animals, pearl prices fell precipitously and it soon became unprofitable to continue the very expensive hard-hat diving operations. Although a secondary market existed for the mother of pearl shells, these weren't worth enough on their own to keep the diving industry alive other than a very limited demand for large wild-caught oysters which could be used to culture very big pearls or several pearls per animal. As a result, shells available in modern times have become progressively smaller. Wild shells would commonly reach sizes of over 10" and 2 lbs., compared to 6" and only .5 lb. currently.
There were also other traditional oyster or abalone fisheries employing native free divers in the Philippines, Indonesia, Tahiti, New Zealand, and to a lesser extent in Panama, Venezuela, Mexico, and even North America.
All oysters are bivalves (two shells hinged together), with the bottom or "right hand" half flatter and less domed than the top "left hand" valve. The best and largest pure white MOP nacre comes from Australia's Silver-Lip Ocean Pearl Oyster (Pinctada maxima); gold MOP from the Yellow-Lip in Indonesia and the Philippines (also P. maxima); and black material from Tahiti's Black-Lip (P. margaritifera). The gold and black species have a white interior, but with a colored layer between the white and the outer non-pearly "bark" of the exterior.
Worldwide, there are about 80-100 species of abalone, a 1-shelled univalve snail (a gastropod = "stomach foot", because they crawl on their belly). Most are too small, thin, colorless, rare, or endangered for commercial use, with only 6 or 7 large and thick enough to make solid flat blanks for inlay work. They have always been harvested primarily for food, but every culture has also valued the shells or things made from them for personal ornament, trade goods, or even actual currency (such as Native American "wampum").
Since abalone are typically found in very shallow or intertidal waters out to depths of around 100', collecting by hand has always been relatively easy without any special equipment, especially during low tides. So, native fisheries have existed since prehistoric times, and archaeologists have discovered gigantic shell piles known as "middens" all over the world. Commercial fishing in the 20th century employed hard-hat diving, and to such an extent that many traditional beds have suffered ecological damage. The California abalone fishery has been permanently shut down since 1997, and free-diving (using only a snorkel but no supplied air) for sport caught animals has seen increasing restrictions and is currently closed until at least 2026 to allow populations to recover from several natural environmental stressors (not just overharvesting).
Oyster and abalone fisheries in Mexico's Baja peninsula, New Zealand, Tahiti, Japan, Australia, the Philippines, Indonesia, South Korea, and other places have sustainably managed beds that include size and seasonal limits as well as re-seeding farm-raised juveniles to ensure healthy future populations. There are also several places globally which are successfully raising animals which have never been in the wild – since these operations are strictly for meat, the animals are never grown large enough for commercial shell use since after the first several years growth becomes too slow to return a profit for the costs involved.
For information on other species of pearlescent marine shells, see: "Shell Names, Origins, and Notes".
CLEANING, DYING, AND POLISHING SHELL
Shells and Mother of Pearl – Knowledge Base
What methods can be used to clean and polish a raw, whole, abalone shell for display?
NOTE: Since the following techniques may involve the use of power equipment and chemicals, this information is being offered for educational purposes only and we will not be held responsible for any health or medical consequences, or material damages. Any application of this information is entirely at the user’s own risk.
That said, it should be noted that proper precautions must always be used when dealing with shell to protect from dust inhalation, such as working out of doors, using fans or vacuums to clear away any dusts or fumes, using a good, tight-fitting rubber dust mask (not the cheap paper “surgical-style” masks which leak around the edges and are virtually worthless), regular cleaning of the work area, and laundering of dust-laden work clothing.
When using power tools or equipment, gloves and eye protection are strongly suggested. When using acids, always use chemical-resistant gloves, eye protection, and aprons, have a source of running water handy, and make sure there is adequate ventilation to quickly remove fumes from the work area; to prevent violent and dangerous chemical reactions, never add water to acid, but always add acid to water.
To smoothly expose the pearly layer of a shell on it’s backside:
1) Use a stick or small hammer to knock off any barnacles or worm-tubes.
2) With a bench or hand-held grinder quickly and crudely remove all or most of the non-pearly outside conchiolin (or "bark").
3) Power-sand with very coarse sandpaper until the grinder marks are completely gone and the back is evenly domed, followed by hand or power sanding with increasingly fine grits of paper all the way down to 220, 400, and 600. Before progressing to the next grit, it’s important to make sure all the scratches from the previous grit have been removed. With the 600, first sand completely using dry paper, then repeat using it wet.
4) Use a soft rag buffing wheel generously charged with white rouge (known to jewelers as "zam") to bring up a glassy finish.
5) Use warm soapy water and an old toothbrush to clean away any remaining buffing compound, especially in small holes or cracks, then rinse and dry thoroughly.
6) Using a soft-bristled paint or basting brush to get into all the little cracks and holes, apply a light rub of mineral oil inside and out, let sit overnight, wipe off the excess with a lint-free rag, and it's done! It's considered very amateurish to ever coat a serious display or specimen shell with any type of lacquer or epoxy, which creates an unnaturally artificial-looking surface and will usually eventually turn yellow or cloudy and thus defeat what you're trying to accomplish. Mineral oil is all that's necessary.
To reveal the natural 3-D undulations in the backside’s underlying nacreous layer:
For a very pretty and more natural-looking effect, use this alternative prep method in which all the backside bark is removed without grinding (most effective for a younger, solid, shell that has a complete and unworn outer bark layer, and no boring clam holes penetrating through it):
1) Knock off any unwanted barnacles or worm tubes, and then pick off the remaining small bits using the point of a knife or any sharp pointed steel tool, and scrub clean with a stiff steel wire brush.
2) Carefully and completely coat all the visible pearlescent surfaces on the inside of the shell with a heavy coat of Vaseline jelly, being very careful to not get any jelly on the shell’s backside – if you do, it must be completely removed or it will prevent the acid from eating into the bark at that spot (the Vaseline acts as a “resist” to the acid).
3) Unless you have a good laboratory-style hooded vent fan, this step should always be done out-of-doors: use a simple brass or copper S-hook (not steel) to lower the shell into a plastic paint bucket containing enough muriatic acid (used to clean swimming pools, and available at a paint store) to totally cover the shell (this process will create an alarming pink and green foam, and fumes that you need to avoid breathing). Check on it every 15 minutes or so by lifting out with your brass hook, until all or most of the bark has been eaten off.
4) Remove, rinse well under running water, and then wash in warm soapy water to remove all the Vaseline. Rinse again in clean water while scrubbing inside and out with a rag or soft bristle brush to get rid of any thin whitish film which may remain.
5) Dry the shell in the sun, or in a kitchen oven on the lowest or pilot-light setting and with the door cracked open.
6) When totally dry and still warm (if no further ornamental carving is still to be done), use a basting brush to apply a thin coat of mineral oil inside and out, working it into every corner, hole, and crevice, let stand overnight, and finish by wiping off all excess oil with a soft, lint-free rag.
To professionally clean and brighten up a "raw" specimen or display-grade abalone shell:
1) Knock off any unwanted barnacles or worm tubes, and then pick off the remaining small bits using the point of a knife or any sharp pointed steel tool, and scrub clean with a stiff steel wire brush (this initial prep work is critical to success and can take up to an hour). If the shell has especially interesting or large barnacles or worm tubes, these may be left on while everything else is cleaned away.
2) Unless you have a good laboratory-style hooded vent fan, the next step should always be done out-of-doors: use a simple brass or copper S-hook (not steel) to lower the shell into a plastic paint bucket containing enough muriatic acid (used to clean swimming pools, and available at a paint store) to totally cover the shell, but for no more than 10-15 seconds, as longer immersion will cause damage and roughen the inside surface texture (this process will create an alarming pink and green foam, and fumes that you need to avoid breathing).
3) As soon as it's lifted out of the acid, hose it off thoroughly with water while scrubbing inside and out with a rag or soft bristle brush to get rid of the very thin whitish film which remains.
4) Dry the shell in the sun, or in a kitchen oven on the lowest or pilot-light setting and with the door cracked open.
5) When totally dry and still warm, use a basting brush to apply a thin coat of mineral oil inside and out, working it into every corner, hole, and crevice, let stand overnight, and finish by wiping off all excess oil with a soft, lint-free rag. It'll look like it just came out of the sea!
How is worked or carved shell polished?
Below are a compilation of methods from books and shell workers.
NOTE: Since the following techniques may involve the use of power equipment and chemicals, this information is being offered for educational purposes only and we will not be held responsible for any health or medical consequences, or material damages. Any application of this information is entirely at the user’s own risk.
That said, it should be noted that proper precautions must always be used when dealing with shell to protect from dust inhalation, such as working out of doors, using fans or vacuums to clear away any dusts or fumes, using a good, tight-fitting rubber dust mask (not the cheap paper “surgical-style” masks which leak around the edges and are virtually worthless), regular cleaning of the work area, and laundering of dust-laden work clothing.
When using power tools or equipment, gloves and eye protection are strongly suggested. When using acids, always use chemical-resistant gloves, eye protection, and aprons, have a source of running water handy, and make sure there is adequate ventilation to quickly remove fumes from the work area; to prevent violent and dangerous chemical reactions, never add water to acid, but always add acid to water.
Old traditional methods:
From “The Birmingham Pearlies”, by Sue Perfect, 2001, concerning fancy English shell work in the 1800’s and early 1900’s:
P. 128:
Polishing
Friction is the key to polishing pearl but in order to obtain a highly polished surface it has to be reasonably flat. Pumice, emery powders, grinding and facing allow this to be successful while, for the final polish, Oil of Vitriol [sulfuric acid] is applied by hand or sometimes left for awhile ‘faking out’ for the corrosive agents to work. With the progression to barrel polishing, a combination of saw-dust and wax shavings were added to small items which were put together with small pieces of scrap pearl [and] this mixture polished itself.
P. 146:
…the corrosive properties of sulphuric acid are used to polish the pearl. Together with the barrel polishing described in the chapter on buttons these methods represent techniques used in France and guarded zealously for many generations.
P. 147:
When pearl is soaked in sulphuric acid the various layers that make up the pearl begin to separate. The process is very slow and takes many weeks to achieve unfortunately the resulting layers are unworkable. Pearl can of course be mopped to a high finish but is more time consuming than putting the objects in a bowl of acid for a short time or stroking the pearl with a [cotton] rag that has been soaked in acid.
P. 156:
The finished [MOP] handle would not have been polished in a barrel but would have, years past, been hand polished sometimes using an acid soaked rag. While I was discussing this matter with my father an amusing conversation developed! “What about the acid burning the skin?” I asked. “Well,” says my father, “You’d wrap the rag around a stick first, wouldn’t you?”.
Old friend John Emr (now deceased), one of two partners who owned Cresthill Industries in Yonkers, NY, a large old pearl button manufacturing company, says finished buttons were polished by barrel tumbling them in sawdust dampened with sulphuric acid. This is also a technique presented in “Histoire des Eventails”, by Spire Blondel, Librairie Renouard, Paris, 1875, a French book about the old tabletterie town of Meru.
Modern methods:
After finely sanding to remove all scratches, use Zam polishing/buffing compound, available either in a solid bar or a tube. Red jewelers rouge is also good, as long as there aren’t any worm holes or seams that will trap and hold the color which can be a hassle to remove.
When was dyed shell first used in folding hand fans?
Referencing Spire Blondel’s 1875 book (“Histoire des Eventails”, S. Blondel, Librairie Renouard, Paris), in the chapter on Mother of Pearl he says:
“…none of these mother-of-pearls is as successful as the nacre d’Orient, called Goldfish which has caused a revolution in the luxury fan industry during the last few years. Thanks to a process invented by Mr. Meyer, all the rainbow shades can be imparted to this remarkable product.”
The “process invented by Mr. Meyer” is in reference not to “Goldfish” per se as a certain type of shell, or as a particular variety of backing veneer, or even as a novel technique for working shell, but is instead addressing a then-new method of using aniline dyes to brilliantly stain shell. In other words, Blondel is talking about Meyers’ dyeing process as being applied to an already particularly popular shell, by way of illustration, known as Goldfish; but “Goldfish” refers very specifically not to Meyers’ actual process but to material taken from the Japanese Awabi abalone, Haliotis gigantea, which is characterized by a distinctive “washboard” or “fiddle back” rippled figure that is unmistakable and thus easily identifiable, and is by far the shell most often seen dyed when used in fans, whether in the sticks or as backing veneers.
Blondel’s statement is almost identical to an entry presented in the Dictionnaire Encyclopédique et Biographique de l'Industrie et des Arts Industriels, edited by Eugène-Oscar Lami, published by Librairie des Dictionnaires, p.734, which was published 11 years after Blondel, in 1886:
“…none of these pearly shells merits greater popularity than the oriental mother-of-pearl called goldfish, which over the last twenty years or so has caused a revolution in luxury fan-making. Using a process resulting from the use of aniline dyes, of which Mr. Meyer is the inventor, it has been possible to impart all the shades of the rainbow to this remarkable product. – s.B.”
Thus, Lami establishes that “Goldfish” shell had been widely popular in fans “over the last twenty years or so”, or roughly from around 1866. This species of shell is the “remarkable product” which 9 or 10 years later Blondel says it’s been “possible to impart all the shades of the rainbow” “to” with a more recent coloring process. That new dye was a type of aniline.
Aniline was first isolated from the destructive distillation of indigo in 1826 by Otto Unverdorben (Pogg. Ann., 1826, 8, p. 397), who named it crystalline. In 1834, Friedrich Runge (Pogg. Ann., 1834, 31, p. 65; 32, p. 331) isolated from coal tar a substance which produced a beautiful blue colour on treatment with chloride of lime; this he named kyanol or cyanol. In 1841, C. J. Fritzsche showed that by treating indigo with caustic potash it yielded an oil, which he named aniline, from the specific name of one of the indigo-yielding plants, Indigofera anil, anil being derived from the Sanskrit, dark-blue, and the indigo plant. About the same time N. N. Zinin found that on reducing nitrobenzene, a base was formed which he named benzidam. August Wilhelm von Hofmann investigated these variously prepared substances, and proved them to be identical (1855), and thenceforth they took their place as one body, under the name aniline or phenylamine.
But aniline’s first industrial-scale use was in the manufacture of mauveine, a purple dye accidentally discovered in 1856 by an 18 year old chemistry student, William Henry Perkins (1838-1907). Backed by his father and a brother, it took several years for Perkins to perfect the manufacture of aniline purple, or mauve. Mauve first found widespread use in France, but by 1862 Queen Victoria of the United Kingdom appeared at the Royal Exhibition in a mauve silk gown. Perkins went on to produce numerous other synthetic dyes at his factory, including alizarin [aka Mordant Red or Turkey Red] (from “The Basics of Chemistry”, by Richard Myers, Greenwood Publishing Group, 2003, p.295).
In 1864, a judicial sentence favoring the French company “La Fuchsine”, in a fight over the scope of patents it held on the colorant by the same name, established its almost complete grip on the French dye industry. This put the many French companies constituting the paint and coloring industry on notice, resulting in a large movement of firms to Switzerland, where patents were instead illegal. From 1864 onward and for about two decades, “La Fuchsine” (“Poirrer”, after the 1868 acquisition) dominated the French market, thanks to its patents (from “Against Intellectual Monopoly”, Boldrin & Levine, 2008, Chapter 9 “The Pharmaceutical Industry”, p.247 & 248).
In 1880, napthol yellow S was issued French patent 134,632. In 1885, tartrazine [a yellow orange dye] was issued French patent 169,964.
All the above is to suggest that dyed shell in fans must date at least a few years prior to 1875 Blondel, perhaps as early as 1870.
Good friend Thomas DeLeo, in personal correspondence, begs to differ regarding such early use of aniline dyes:
“…early aniline dyes were very intense in color: mauve, then yellow, blue etc. The yellow aniline is sulphuric in color and the blue “electric”. These are colors I do not see in fans from 1870’s and earlier. Later in the 1880’s, yes the sticks and guards are often these eye popping colors.”
But in rebuttal, it should be noted that in 1875 Blondel clearly says “all the rainbow shades” were in common usage, a claim later repeated in 1886 by Lami. As for color intensity, that’s true of anilines when freshly applied; but anilines are famous for fading, often drastically, on exposure to ultra-violet. In fact, modern guitar builders sometimes prefer using them for the very reason that the colors will fairly quickly acquire a faded “vintage” look.
What are older methods of coloring or gilding nacreous shell?
Below is a compilation of methods found in old technical books, plus added notes by a professional hand fan restorer.
NOTE: Since the following techniques may require the use of various chemicals, this information is being offered for educational purposes only and we will not be held responsible for any health or medical consequences, or material damages. Any application of this information is entirely at the user’s own risk.
That said, it should be noted that proper precautions must always be used when dealing with shell to protect from dust inhalation, such as working out of doors, using fans or vacuums to clear away any dusts or fumes, using a good, tight-fitting rubber dust mask (not the cheap paper “surgical-style” masks which leak around the edges and are virtually worthless), regular cleaning of the work area, and laundering of dust-laden work clothing.
Soaking in dilute muriatic acid is used to prepare Capiz or “Window” shells (Placuna placenta) for dying but not for molding (soaking too long in the acid will dissolve the calcium carbonate and permanently damage the shells). Boiling will soften Capiz enough to cut with a scissors, but for molding into shapes the dried shells are soaked overnight in a weak solution of hydrogen peroxide. I suppose pressure cooking might be effective for thicker shell, but I haven’t tried that yet. It’s been many years since I worked with Capiz, and can’t remember much detail. So it will take some experimenting.
From: “Mackenzie’s Five Thousand Receipts in All the Useful and Domestic Arts Constituting a Complete Practical Library”, Colin Mackenzie, 1854:
P. 53. Liquid gold for vellum painting. Having procured some of the finest gold leaf, grind it with strong gum-water, adding more gum-water as is found requisite; when thoroughly ground temper it with a small quantity of sublimate of mercury, binding it in the shell with a little dissolved gum; spread it equally over the shell, and use it with water only, for gilding fans, &c.
P. 53. Liquid silver for the same. The manner of making this is the same as that of liquid gold, only remembering to temper it with glaire of eggs, and not water.
P. 53. To make glaire of eggs. Beat the whites with a spoon till they rise in a foam; let them stand twelve hours, and they will be clarified into good glaire.
From: “The English and American Mechanic”, B. Frank Van Cleve, 1874:
P. 180. Silvering Shells. Silver-leaf and gum water a sufficient quantity; grind to a proper thickness, and cover the inside of the shells. For a gold color, grind up gold-leaf with gum water, and apply to the inside of the shells.
P. 222. True Gold Powder. Put some gold-leaf, with a little honey, or thick gum-water made with gum Arabic, into an earthen mortar, and pound the mixture till the gold is reduced to very small particles; then wash out the honey or gum repeatedly with warm water, and the gold in powder will be left behind. When dry, it is fit for use.
P. 223. General Directions for Bronzing. The choice of the above powders is, of course, determined by the degree of brilliancy you wish to obtain. The powder is mixed with strong gum-water or isinglass, and laid on with a brush or pencil; and, when not so dry as to have still a certain clamminess, a piece of soft leather wrapped round the finger is dipped in the powder, and rubbed over the work. When the work has been all covered with the bronze, it must be left to dry, and any loose powder then cleared away by a hair-pencil.
From: “The Techno-Chemical Receipt Book”, Winckler, Elsner, Heintze, Mierzinski, Jacobsen, Koller, Heinzerling, Brannt, and Wahl, 1886:
P. 104. To Dye Mother-of-Pearl with Aniline Colors. Wash the thin plates with lukewarm solution of potash, then place them in a concentrated aqueous solution of the coloring matter, and let them stand in a warm place, frequently stirring them. If the dye is to penetrate to some depth the plates must remain in the coloring matter for two weeks, then be rinsed and dried.
From: “Encyclopedia of Practical Receipts and Processes”, William B. Dick, 1903:
P. 6187. To Color Shells. Dissolve a little lac dye in a solution of chloride of tin; and having made the shells thoroughly clean, dip them in this preparation until they are of the desired color. The dye should be first boiled, and then allowed to stand to settle.
From: “Scientific American Cyclopedia of Formulas”, edited by Albert A. Hopkins, 1910:
P. 590 (3). Iridescent. The following is said to be the process used in the Vienna shell button works. In a wide-mouth jar large enough to hold the shells, and fitted with a ground glass stopper, put as much ammonia water as will cover the shells. To this add silver chloride in powder until the liquid becomes saturated and a slight excess of the silver salt is established. Into this put the shell and, applying the stopper, set aside in a dark place for a few days. The play of colors is usually established in a few hours, but its permanency is made surer by a little longer exposure to the sun. As a general rule, one week’s contact with the ammonia water, with two days’ exposure to the direct light, are all-sufficient.
From: “Department bulletin”, United States Dept. of Agriculture, 1918, p. 8:
The following patents for the preparation of napthol yellow S were issued in 1880: French patent 134,632.
In 1885 the following patents for the preparation of tartrazine [a yellow orange dye] were issued: French patent 169,964.
From: “The Basics of Chemistry”, by Richard Myers, Greenwood Publishing Group, 2003, p.295 [Notes on the 1800’s French aniline dye industry]:
William Henry Perkins (1838-1907)…Backed by his father and a brother, Perkins established a dye plant in London and obtained a patent for aniline purple or mauve. It took several years for Perkins to perfect the manufacture of mauve, and in the process, he had to convince the textile industry of the advantages of his synthetic dye. Mauve first found widespread use in France, but by 1862 Queen Victoria was wearing a dress dyed with mauve. Perkins went on to produce numerous other synthetic dyes at his factory, including alizarin. The synthetic production of alizarin [aka Mordant Red or Turkey Red], a red dye, ruined the farming of madder in the Provençe region of France.
From: “Against Intellectual Monopoly”, Boldrin & Levine, 2008, Chapter 9 “The Pharmaceutical Industry”, p.247 & 248 [Notes on the 1800’s French aniline dye industry]:
At its inception, the dye industry was a French-British business the same way that almost any industry was a French-British business until the second half of the nineteenth century. In both countries patent protection applied to all kinds of industrial products. In 1862 British firms controlled about 50% of the world market, and French firms another 40%, Swiss and German companies being marginal players. By 1873 German companies had 50% of the market, while French, Swiss and British firms controlled between 13% and 17% each.
In that year [1864], a judicial sentence favoring the French company “La Fuchsine”, in a fight over the scope of patents it held on the colorant by the same name, established its almost complete grip on the French dye industry. This put the many French companies constituting the paint and coloring industry on notice, resulting in a large movement of firms to Switzerland, where patents were instead illegal. From 1864 onward and for about two decades, “La Fuchsine” (“Poirrer”, after the 1868 acquisition) dominated the French market, thanks to its patents.
From: further notes through personal correspondence with fan restoration expert Betsy Smith:
I have examples of antique fans which are dyed: two peacock blue, two purples, a real bright yellow, an orange, and a sweet pink.
Aniline
History: Aniline was first isolated from the destructive distillation of indigo in 1826 by Otto Unverdorben (Pogg. Ann., 1826, 8, p. 397), who named it crystalline. In 1834, Friedrich Runge (Pogg. Ann., 1834, 31, p. 65; 32, p. 331) isolated from coal tar a substance which produced a beautiful blue colour on treatment with chloride of lime; this he named kyanol or cyanol. In 1841, C. J. Fritzsche showed that by treating indigo with caustic potash it yielded an oil, which he named aniline, from the specific name of one of the indigo-yielding plants, Indigofera anil, anil being derived from the Sanskrit, dark-blue, and the indigo plant. About the same time N. N. Zinin found that on reducing nitrobenzene, a base was formed which he named benzidam. August Wilhelm von Hofmann investigated these variously prepared substances, and proved them to be identical (1855), and thenceforth they took their place as one body, under the name aniline or phenylamine.
Its first industrial-scale use was in the manufacture of mauveine, a purple dye discovered in 1856 by William Henry Perkin.
p-Toluidine, an aniline derivative, can be used in qualitative analysis to prepare carboxylic acid derivatives.
Toxicology: Aniline is toxic by inhalation of the vapour, absorption through the skin or swallowing. It causes headache, drowsiness, cyanosis, mental confusion and in severe cases can cause convulsions. Prolonged exposure to the vapour or slight skin exposure over a period of time affects the nervous system and the blood, causing tiredness, loss of appetite, headache and dizziness.[2]
Oil mixtures containing rapeseed oil denatured with aniline have been clearly linked by epidemiological and analytic chemical studies to the toxic oil syndrome that hit Spain in the spring and summer of 1981, in which 20,000 became acutely ill, 12,000 were hospitalized, and more than 350 died in the first year of the epidemic. The precise etiology though remains unknown.
Some authorities class aniline as a carcinogen, although the IARC lists it in Group 3 (not classifiable as to its carcinogenicity to humans) due to the limited and contradictory data available.
Mauveine
Mauveine, also known as aniline purple, was the first synthetic organic dye [1] [2] . The chemical name is 3-amino-2,±9-dimethyl-5-phenyl-7-(p-tolylamino) phenazinium acetate. The formula is C26H23N4+X− (mauveine A) and C27H25N4+X− (mauveine B, see below).
It was discovered serendipitously in 1856 by an 18-year old William Perkin, who was trying to synthesize the anti-malaria drug quinine as a challenge offered by his professor, August Wilhelm von Hofmann. In one of his attempts related to the quinine challenge, Perkin oxidized aniline using potassium dichromate. Under these conditions, the aniline reacted with toluidine impurities in it to produce a black solid, a fairly common result in "failed" organic syntheses. However, while trying to clean out his flask, Perkin discovered that some component of the black solid dissolved in alcohol to give a purple-coloured solution, which proved to be an effective dye for silk and other textiles.
Perkin patented the new dye and the next year, he opened a dyeworks at Greenford on the banks of the Grand Union Canal in London in order to mass produce it. Mauve became highly fashionable in 1862 when Queen Victoria of the United Kingdom appeared at the Royal Exhibition in a mauve silk gown. Mauve fell out of fashion in the late 1860s to newer synthetic colors, but not before making Perkin's fortune and birthing the synthetic chemical industry. Later work on chemical dyes also led to the (accidental) development of modern chemotherapy (see Sulfonamide).
Uses: Originally the great commercial value of aniline was due to the readiness with which it yields, directly or indirectly, valuable dyestuffs. The discovery of mauve in 1856 by William Perkin was the first of a series of dyestuffs which are now to be numbered by hundreds. Reference should be made to the articles dyeing, fuchsine, safranine, indulines, for more details on this subject. In addition to its use as a precursor to dyestuffs, it is a starting-product for the manufacture of many drugs such as paracetamol (acetaminophen, Tylenol).
It is used to stain neural RNA blue in the Nissl stain.
Currently the largest market for aniline is preparation of methylene diphenyl diisocyanate (MDI), some 85% of aniline serving this market. Other uses include rubber processing chemicals (9%), herbicides (2%), and dyes and pigments (2%). [1]
Mauve: Mauve\, n. [F., mallow, L. malva. So named from the similarity of the color to that of the petals of common mallow, Malva sylvestris. See Mallow.] A color of a delicate purple, violet, or lilac. Mauve aniline (Chem.), a dyestuff produced artificially by the oxidation of commercial aniline, and the first discovered of the so-called coal-tar, or aniline, dyes. It consists of the sulphate of mauve["i]ne, and is a dark brown or bronze amorphous powder, which dissolves to a beautiful purple color. Called also aniline purple, violine, etc.
WORKING WITH TRADITIONAL SOLID SHELL BLANKS
Shells and Mother of Pearl – Knowledge Base
What's a good source for bright solid color inlay material such as blue, yellow, red, orange etc. ?
No actual sources for bright colored materials. Some inlayists such as Craig Lavin (Handcraft Inlay) [use live link from "Industry Sources"] use epoxies, casting resins, Sculpey® Clay, and other craft substances – either to fill a routed cavity, or cast into small blocks which can be cut into slabs. Larry Robinson [use live link from "Industry Sources"] likes to go to yard sales and pick up brightly colored plastic toys that can be sawn up. Masecraft Supply Co. [use live link from "Industry Sources"] has a wide selection of synthetic products for knife handles and inlay work.
How are flat blanks and dots made from raw shells?
To make flat blanks (needed for dots) cut the raw shell into pieces small enough to be then flattened into uniform thickness. The photos below display how shells are cut into large sections which are then trimmed and cut into smaller pieces:
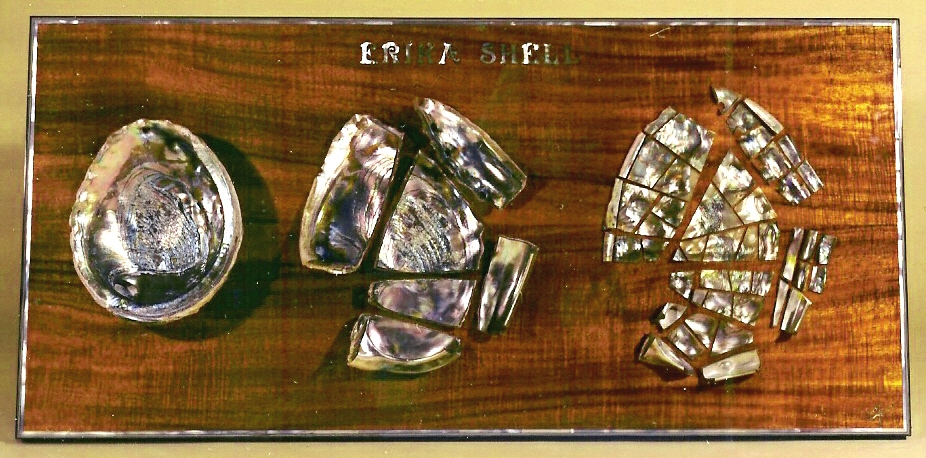
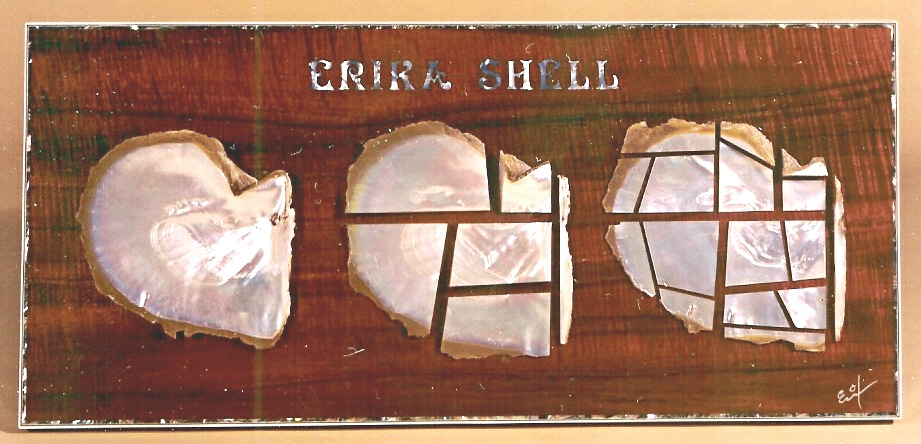
For just a shell or two this can be done with a hacksaw, a fine toothed bandsaw or heavy jigsaw (working dry), or a circular abrasive carborundum or diamond blade (preferably working wet). The resulting pieces would then have their concave sides flattened on the side of a grindstone. They would next be passed through a thicknessing sander, grinder, or saw to remove the unworked backsides and get the desired uniform thickness – this can also be done crudely by eye on a grinder or belt sander.
These flat blanks would then be ready to cut into dots using any of various hole saws/plug cutters (toothed or abrasive). If only doing a small number of dots you could cut the blanks into small squares of proper size, and glue these on the end of a short dowel section (known in the jewelry trade as “dopping” on a “dop stick”). Chuck the dowel in a drill press and while the piece is spinning use a file to shape the pieces down to size – a simple backstop can be set up to control the diameter for uniform sizes. When done, soak or pry the dots free of the dowel.
Since manufactured shell dots of all sizes are readily and cheaply available, the above process is a tremendous amount of hassle and stink to put up with unless you’re just in it for the questionable spiritual mojo of doing everything yourself by hand and don’t care about efficiency or wasting a lot of time. For a garage hobbyist this might be somewhat understandable; but for a busy professional shop it wouldn’t make much sense unless just philosophically intent on at least once getting the primal experiences with one’s materials!
How long does it take to make flat blanks from a shell?
- A) Be careful what you ask for, as you'll usually get more information than you needed to know! Traditional solid blanks are the simplest product. Back in the 1990's when I was personally processing tons of material, here's what the numbers looked like.
WHITE M.O.P. OYSTER SHELL, best grade, 100 lbs., 58 shells. Ocean Pearl Oyster is a bivalve, but since the top half is more domed than the lower valve, we use only the flatter "right hand" half. The domed "left hand" valve is used only when shells become difficult to procure in the quantities needed, but average blank size will be reduced.
Yield: 11.63% by weight (88.37% scraps and dust) = 11.63 lbs. of #1 grade blanks = 1,509 blanks (about 8/ounce).
Time: 23.32 hours = 4.29 lbs. (or 2.49 shells)/hour = 24.1 minutes/shell = 55.63 seconds/blank (or 7.52 minutes/ounce).
RED ABALONE SHELL, top grade, 100 lbs., 80 shells. All abalone are snails, a univalve with only a single shell.
Yield: 7.25% by weight (92.75% scraps and dust) = 7.25 lbs. of #1 grade blanks = 1,848 blanks (about 16/ounce).
Time: 28.6 hours = 3.5 lbs. (or 2.8 shells)/hour = 24.45 minutes/shell = 55.71 seconds/blank (or 14.79 minutes/ounce).
GREEN ABALONE SHELL, top grade, 100 lbs., 106 shells.
Yield: 4.89% by weight (95.11% scraps and dust) = 4.89 lbs. of #1 grade blanks = 2,656 blanks (about 34/ounce).
Time: 28.6 hours = 3.5 lbs. (or 3.71 shells)/hour = 16.17 minutes/shell = 38.77 seconds/blank (or 21.93 minutes/ounce).
Since then, available shell sizes/weights have become much smaller, taking proportionately more time and yielding fewer and smaller pieces, while raw shell prices have climbed by over 1,000%. All the shells we process are of legal size, legally harvested, and with a fully documented paper trail; but the sometimes huge old wild-caught shells from decades ago have been replaced with sustainably managed or farmed animals which are harvested at younger and smaller sizes.
Our production methods now use more sophisticated (and safer!) equipment but almost everything is still by hand with no automation involved. Of course, most of our work now is making veneer and Abalam® sheets, and although this increases actual yields by 400-500% the process is much more skilled and labor intensive, making cost analysis/pricing vastly more complicated!
How do you grade or sort solid shell blanks?
Before discussing solid shell it should be mentioned that Abalam® is not intended to replace these but to add a much broader choice of materials, make certain types of work more esthetically pleasing, and greatly reduce the amount of time involved in such tasks as doing shell guitar bindings or full length fingerboard vines.
But traditional blanks may still be preferable to laminates for some applications, mainly because they can yield a range of color and figure choices not possible otherwise. Blanks are generally available in carefully hand-sorted grades such as:
Regular #1.
Large.
Extra Large.
Select best color.
Select best figure (in White MOP only).
Plain, no figure (in White MOP only).
Sunburst (in gold and black MOP).
Unsorted (in White MOP only).
Heart figure (in abalone only).
Rippled figure (in Green ab. only).
Pale (in Red ab. only).
The above selections are perfectly suited to the way most inlays are done. But top artists such as Grit Laskin, Larry Robinson, Dave Nichols, Harvey Leach, Arianna Colombo, Renee Karnes, Craig Lavin, Paul Bordeaux, and a few others spend extra effort in matching very specific pieces of shell to each element in an inlay pattern. To this end, solid shell can be further sub-graded into such personally idiosyncratic categories as these examples (my personal system) for only 2 shell species:
For White MOP:
Plain, dead white.
Plain, intense red flash.
Plain, intense green flash.
Figure with intense color.
Small fleece figure.
Medium fleece figure.
Large fleece figure.
Finger figure.
Wavy figure.
Fan figure.
Eye figure.
Dome figure.
Odd figure.
Wrinkled (“fingerprint”) figure.
For Green Abalone:
Intense pinks.
Intense greens.
Intense blues.
Intense violets.
Rainbow (half blue, half pink).
Pale figured.
Pale unfigured.
Broadly striped figure.
Finely striped figure.
Broad ripple figure.
Fine ripple figure.
Regular heart figure.
Crinkled heart figure.
Bull’s eye figure.
Eye figure.
Frog figure.
Dome figure.
Odd figure.
Wrinkled (“fingerprint”) figure.
As far as shell choices in inlay, there are two basic approaches: 1) designing an inlay and then finding pieces which will fit the pattern; 2) being aware of particular pieces of shell and then designing inlay around what’s found in those pieces, what the piece of shell itself suggests. For most inlayists working with a limited amount of shell on hand, option 2 just isn’t practical, although color and figure choices can still be consciously controlled in a limited sense.
But even when dealing with smaller amounts of shell, it may be worthwhile to start sorting out pieces which for one reason or another are noticeably different than everything else – over time, an impressive “stash” of very unique pieces will accumulate which can be used in special projects. Generally, the more shell an artist has on hand to select from, the more control can be exercised over the final results.
We have a "Shell Cutter's Stash" [use live link from product listing] poster available that shows examples of the above personal grades.
How do you define your Green Abalone blank grades?
Grading is tricky, since it’s a subjective “sliding scale” that’s always relative to what’s in each large production run of blanks (which can be different each time, depending on the shells available to be processed at that moment). The main thing is to have very high grading standards and be honest about not letting them slip just because there aren’t enough blanks! Here’s what I’m looking for:
Heart: Must cover 75-100% of one side, not have weak figure, not have a lot of black, and with no worm holes, pits, cracks, or other flaws.
Select Color: Must have exceptionally bright and dense color covering all or most of one side, with the deep coloration going all the way through the blank and showing on at least 50% of the backside (so it can’t easily be sanded away when dressing an inlay flush to a surface), and no flaws.
Rippled: Many or even most blanks will have ripple figure, but to be a special grade the ripple must be smaller or tighter, cover the entire front and most of the back, and be totally clear with no black lines (what we call “100% clear white rippled”), with no flaws.
Large: In 4 lbs. (2 KG) of blanks, these might be 30 or 40 of the biggest pieces, with no or very few flaws. Large Heart, Select Color, and Rippled are worth more than just a large regular piece of shell.
Extra Large: Maybe the 4 or 5 biggest pieces of the above Large.
What's the best way to use different types of shell?
Here are some guidelines that may help in narrowing choices down. But, in the words of Pablo Picasso (the "Picasso Principle"): "Learn the rules like a pro, so you can break them like an artist."
Which laminates require a finish to look best? White/Gold/Brown/Black MOP, Donkey Ear Ab., Agoya shell, paler Red Ab.
Which laminates show most joints? White/Gold/Brown/Black MOP, Japanese Awabi ab., palest Red ab., Green ab. Standard/Rippled. These are best used in smaller or thinner parts, unless such a large area is being covered that it would need to be pieced together anyway.
Figured or plain MOP? Avoid figure in small or delicate/thin parts, since it tends to disrupt the pattern; but strong figure is O.K. in larger/thicker parts.
When engraving, it’s usually best to stick with relatively unfigured MOP and use the plainest shell. It will not only engrave much easier but the inscribed detail will stand out more clearly.
Using figure/color to suggest details (especially when using solid shell). For 3-D effects, roundness can be suggested by carefully laying out inlay over types of figure in MOP which show movement (“domes”, “fingers”, “eyes”, fleece”, “ripple”, etc.). Especially in representational inlays (scenes, clouds, people, animals, trees, etc.) shell which has fine internal texturing can suggest tiny details which aren’t really there, such as musculature, facial features, feathering, fur, moon cratering, etc. See any work by Grit Laskin or Arianna Colombo [use live link from Source List/Hand Inlay Cutting], who are masters at these techniques.
Shadowing can be suggested by using “sunburst” gold or black MOP, which has light areas strongly and abruptly shading to darker. Example: stones, planets, or other objects which are shaded on their unlit sides. This can also work for animals which have dark backs and paler bellies; or partially reflective glass.
Combine or blend similar or contrasting colors to create visual interest:
1) White MOP dots shading from no color flash through increasing shades of pale gold, red, green, blue, and back again.
2) A vine using white MOP, Green Snail, pale Gold MOP, pale Red Ab., and progressively darker abs. which gently grade into each other going from lightest to darkest (or from light, to dark in the middle, and back to light again).
3) With edge strips, picking out those which are pale at one end and dark at the other, joining light-to-light and dark-to-dark ends creates a wonderful regularly-alternating visual "pulse" in the binding.
4) Again, with edge strips, by using a selection of several different shell types, they can be combined so that the color on each side of a top gradually changes from very pale to very dark in a tightly controlled manner. For instance, on each side of the guitar, start at the neck with pieces of very pale and colorless Red Ab.; then pale Red having more colorful flash; then a piece of highly colored pale which has a bit of slight darker figure on one end; then a piece with matching figure which gets even darker at the far end; then some fully dark Red Ab; then pieces of medium density Green Ab.; then darker Green Ab.; then Paua which is predominantly green but leads into the blues; then strongly blue Paua; finally, some Paua Heart. All these pieces should have one end that closely matches the previous strip, which necessitates laying them out in sequence after trimming and squaring to fit each other (keep them in order and right side up by placing on a length of masking tape with the sticky side up). A variation would be to go from heart figure to ½-heart to no heart. It's a great effect that will be very rarely seen (unless you all decide to start doing it!).
When doing multi-piece inlays, shells that either visually clash or blend too much when used next to each other can be given a controlled separation by using black gaps or filled engraved lines over the joints (see any of Grit Laskin’s inlay work for excellent examples).
Control the play of light. For instance, shell inlays can be laid out on an instrument fingerboard so that they sequentially “light up” as the instrument is moved, causing the light to “roll” up and down the neck. Lay blanks out under a one-bulb light source so you can see how they reflect both from a single viewing position, or by viewing at different angles.
A “pulsing” effect can be achieved by having adjoining pieces of shell light up at different times: as one lights up the other goes dark, creating an illusion of movement or a pulsing change in relative size.
Are highly figured or plain MOP shell blanks preferred by most guitar makers? And does the best figure come from large or small shells?
Actually, both small and large shells produce plain and figured material. It is not dependent on shell size, but on where in the shell the material is taken from: the plain unfigured blanks come from the large, flat outer “rim” area of shells, and the figured blanks come from the thicker area next to the “notch” at the top of the straight “hinge” edge and from around the oval muscle scar area where the animal was attached.
Some guitar makers prefer MOP with lots of figure, especially if used in larger sized inlays (such as square block shapes) that are big enough to allow the figure to be seen. On the other hand, plain shell is almost always favored for doing more delicate inlays (such as floral vines, script letters, and most peghead logo names) because if they contain figure the uneven light and dark areas of the figure visually break up and obscure the shape of the inlays, making it harder to see their pattern (sort of like camouflage).
But not all builders want figured shell for large inlays. Because many of the older guitars (such as were made by the Gibson and National Resophonic guitar companies) had simpler inlays made from plain shell, or even mixed plain and figured pieces, builders who like a “vintage” look often will use mostly plain unfigured MOP.
Another consideration is whether or not the inlay will contain fine engraved or saw-cut details. If so, plain shell is almost always preferred because figure creates a couple of problems:
1) It will visually interfere with being able to see the engraved detail.
2) It’s more difficult to do engraving on highly figured shell because the changing grain direction causes it to chip more easily, and also makes it harder to control the point of the graver to get smooth straight or curved lines.
So there’s no general rule about preferences because luthiers have different personal tastes or need either plain or figured shell for certain projects. What we do is offer regular blanks containing a normal mix of plain and figured MOP. But for those with specific preferences we also have special grades of both plain and figured. The “Select Figured” are those very few pieces which have the finest and most intense grain which goes all or most of the way through the thickness of the blank (so it will not easily sand away); the “Select Colored” are the few pieces which are very plain but also have the most intense colorful iridescent “flash”, and which goes all the way through the blank.
As far as larger or smaller “fish scale” figuration, smaller and tighter figure usually comes from the smaller shells, but whether this is the best choice or not again depends on personal tastes and the particular inlay design. Whatever type of figure is involved, the very best pieces are those in which the figure has the most visual “depth” and the sharpest edges (sort of like a picture being slightly in or out of focus); and the best of these would be the blanks that also contain iridescent flash along with the intense figure.
What's the best way to match adjoining MOP pieces? I’ve got an inlay design which is bigger than any one piece. I make the joint between pieces in an area of the design that is quite thin yet the joint still sticks out like a sore thumb due to color and pattern mismatch between the two pieces. No problems doing this with abalone of course. Short of buying pounds of pearl pieces and matching two pieces is there anything I can do to make the joints less obvious?
Trying to closely match any type of shell other than the very darkest abalone grades does indeed involve having enough on hand to sort through. I've always been willing and available to do shell matching on special projects, picking ideal pieces for specific inlays if preference notes and full sized artwork are supplied. Pieces are taken from my personal stash of very high grade materials, so there's a modest additional charge for the material as well as the small amount of time involved, but this isn't at all prohibitive. To a lesser extent, our Ducal Nacretory in Maryland can also offer some blank matching from the large inventory held there, since you'll be talking to people who design and fabricate finished custom inlay every day (not simply a sales person!).
In a composite inlay (made from various pieces being joined together in a mosaic style), adjoining pieces can be arranged to meet along a natural line or break within the design itself. When finishing the inlay, lightly engraving over these lines brings both consistency and clarity to the pattern. Grit Laskin's work offers many wonderful examples of this technique (see pages 90, 108, and 123 in A Guitar Maker's Canvas).
If more than one piece of shell is necessary for making an unbroken larger area than can be done with only a single piece, it helps greatly to reduce the join line as much as possible. With white M.O.P. this would involve matching the internal figure, the iridescent color flash (if any), and the "orient" (how the pieces light up or darken as the viewing angle shifts). Butting two pieces together along a vertical edge will always create a more visible line than if the two edges were skived at an angle and then joined in an overlap; the more they overlap the better, so a very acute angle works best. In fact, this is how the almost invisible joints were made in the 1800's when forming 10"-12" long M.O.P. sticks from 4 or 5 pieces for folding hand fans.
Another option is to use Abalam® (our laminated shell sheets). These are made by stacking several paper thin shell veneer sheets together, each veneer sheet having been made from many smaller pieces of veneer. In the manufacture of each sheet color and figure are matched as much as possible, and then closely matching sheets are assembled in layers. Because the pieces making each layer were arranged with overlapping edges and then sanded down, they're essentially skived together and dark join lines are thus avoided. When trying to cover a large surface such as a peghead, no one expects to see a single uninterrupted piece of shell and multiple pieces are expected. Abalam® is ideal for this application (see pages 74 and 79 in Grit's book).
My specific interest is in the use of abalone (Japanese Awabi w/washboard rippled nacre) for making brisé fans with solid sticks. Can you tell me how this material, coming out of relatively small shells, makes fan guards in excess of 9" long? Do you suppose laminated sections of this MOP were somehow produced back in the day?
Abalone and MOP oyster fan sticks weren’t of laminated shell (as in having thin parallel layers stacked together like plywood, a technique for making the “Abalam®” on which I held 4 U.S. patents). They were made from several shorter pieces of solid shell which were joined end to end by overlapping “scarf joints” of 10° (a 1:7 ratio, which is considered the strongest). These joins can be difficult to spot with a casual glance since much care was taken to closely match figure, color, and reflective angle where the pieces meet. Anywhere from 3 to 6 pieces are common. By the way, this is the same method used in making long tortoiseshell sticks from multiple pieces.
Many years ago the Japanese Awabi was the largest abalone in the world, up to 12” across. But even then, the strong shell curvature and thin internal nacreous layer wouldn’t allow a single flat 9” section to be produced.
There have always been vague rumors of abalone being soaked or boiled in various secret solutions (or even just sea water) for long time periods in order to get shell layers to soften and delaminate into large plates. Based on years of tracking down such stories I can pretty confidently assert this is all totally bogus, although Chinese and Japanese publications were (and still are) totally happy in propagating such myths rather than debunking them, in order for artisans to steer people away from their closely held actual methods. Shell isn't composed of discreet parallel layers, so wouldn't "delaminate" like that anyway. Acid not only won't delaminate any shell, it'll destroy it by dissolving the calcium carbonate and leaving only the skin-like scleroprotein matrix (just as an egg shell can be partially softened with a vinegar soak).
But with very thin saw blades it can be sawn into sizeable veneers following the curve of a shell – we use special .125" wide diamond edged stainless steel bandsaw blades with a .004" kerf. These paper-thin pieces can then either be flattened by pressure cooking, or simply flexed and glued down to a flat surface.
WORKING WITH ABALAM® LAMINATED SHELL SHEETS
Shells and Mother of Pearl – Knowledge Base
What's the difference between real abalone and the Abalam® imitation shell I keep hearing about?
Abalam® IS "real shell", in essence no different than "solid" flat blanks – the only "natural" shell would be the soap-dish job the animal lived in (not limited to abalones, but including oysters, clams, mussels, and others), but from that point on both products are the work of human manufacture. Traditional blanks are cut from a shell and ground flat to many different thicknesses, and even though at some stage of increasing thinness the blanks become known as veneers, this is at best an arbitrary term since it's impossible to exactly define where a "blank" ends and a "veneer" begins! .030" solid material has been used for years, but is .029" stuff then something else? What about .025" thick shell? In fact, this is the top solid and engravable layer found in one form of Abalam® known as Gravlam, which really confuses things! Multi-layered Abalam® proper is shell all the way to the bottom, nothing else in there except the epoxy holding it together, but is composed entirely of thinner pieces (typ. .010") composed into thin layers which are then stacked to get increasing thicknesses.
Not all types of shell are proper for all types of work, as we soon discover. The darker-colored varieties are best when exposed joint-lines will be a problem; lighter types can be best for delicate inlays such as logos or vines; very large inlays are comfortable with either, since these necessarily are a mosaic of smaller pieces and joint-lines are expected to be present. Joint-lines and feathered overlaps in some of the paler shells mostly disappear under a finish, while in others a finish makes no difference. If unfinished, some shells buff-up better than others, and some are more porous. Much of this is covered in our working notes on each type of Abalam®, but distributors of this material seem reluctant to waste catalogue space on such information.
There is also an "upside" and a "downside" ("orient") to all the Abalam® sheets, exactly as there is in the natural shell, and which takes considerable effort to maintain in all the little pieces during manufacture. In addition, the top 2/3 of Abalam® is made from closely-matched shell veneer layers, the bottom 1/3 of poorly-matched or flawed layers, making it even more critical to know which side is "up"! Each 5.5" x 9.5" sheet originally comes with a topside label, but if cut into smaller sections for resale or use this orientation is often not marked on the new pieces, and various problems can result.
Unfortunately, of the 31 "flavors" available in Abalam®, distributors carry only a few, and one of the most popular is "Green Ab. Light" because of it's relative economy. However, for someone first trying a laminate while also trying to save money, this may not be the best choice as it tends to have more visible joints, change color or figure more when sanded down, and have more transparent/interfering layers than do the darker shells. If inadvertently used backside up, the problems are compounded! Thus, a first unsatisfactory experience with laminate can lead to an understandable bias against trying any of the others – a pity since many of the very finest instruments now being made, by small shops as well as large factories, have found extensive technical and aesthetic benefits in adding this material to the inlayist's palette. It would be hard to name a top inlay artist who isn't using Abalam® for something!
We have an "Abalam: A Jubilee" [use live link from product listing] poster available that shows examples of 30 sheet types. Framed and hung in your shop, it's a great resource to have when deciding what to use, or discussing possible shell options with a client!
Which is better – solid shell or Abalam®?
To evaluate the relative importance or impact of Abalam® in luthiery it needs to be thought of not so much in terms of something which is ultimately "good" or "bad" (as though there were a moral “high road”!), but simply as an addition to the existing palette of materials available to a manufacturer or individual inlay artist. It was never intended to replace or make obsolete the use of solid shell. Access to a broad range of materials allows more freedom of expression than would be possible with only a small assortment, but the artist remains the one ultimately responsible for determining which particular ones will be esthetically "right" or "wrong" for any given design. Before the invention of Abalam®, there were only about 12 choices in pearlescent shell materials, from only 5 species of shells – Abalam® has expanded the choices to over 30, taken from 18 species!
It's not uncommon to hear "Abalam® versus the real thing". No one would argue that plywood isn't wood – it's just another form in which wood is available, as opposed to non-woods such as wood-grained plastics or phenolic sheets (or a composition which happens to include, among other things, some wood fibers or chips). In the same way, laminated shell is only another form of "real" shell, not a man-made artificial substance (other than the very minimal amount of epoxy it contains). Thus, it would be less misleading and more accurate to refer to “Abalam® versus solid” or “laminated versus traditional” – just a suggestion which would keep things technically honest and help avoid confusion!
Along with laminated shell products we continue to offer high-grade solid blanks and strips, and openly advise on the advantages and disadvantages of both types of material. Some situations benefit artistically from the use of solid and others from laminated, and some Abalam® is better used under a finish than uncoated (as on most guitar fingerboards).
SOLID SHELL AND LAMINATES COMPARED:
Quality | Solid shell | Abalam |
Density | 100% | 90% |
Thickness | Under .100” | Unlimited |
Inlay size limit (length) | Under 1.5” | 5.25” to 9.25” |
Layout time | Slow | Fast |
Waste produced | Most | Least |
Depth of color & figure | Changes quickly | Minimal change |
Uniformity, color/figure | Highly variable, hard
to control |
Homogenous, predictable |
Visual considerations | Many visible joints in larger inlays | Pale shells: joints, transparency |
Special figure/color grades | Customizable: “bull’s eyes”/“fleece”/“stripes” | Standardized |
Ability to accept buffing | Takes high polish | Varies with type of shell |
Basic choices available | 15 | 30+ |
Internal flaws & fractures | Common | Minimal |
Fragility, hand cutting | Less fragile | More fragile |
Fragility, CNC cutting | More fragile | Less fragile |
Release from backing board | Can be boiled | Boiling will delaminate |
Saw blade & rotary bit life | Shortest | Longest |
Takes finer cut detail | No | Yes |
Engraved detail | Easy | Difficult |
Breaking strips to fit curves | Odd angles/splinters,
less breaks/inch |
Straight across, more breaks/inch |
Material cost only | Cheapest (except for Green ab.) | 20+% more than blanks |
Material + labor cost | Most expensive | Less than blanks |
Impact on shell resources | Minimal yield/more pressure on only 6 species/most wasteful | 400-600% higher yield/less pressure on 18+ species |
What ecological impacts are involved in the manufacturing of Abalam®?
We use 18 species of shell, producing 31 different types of sheets, sized 5.5” x 9.5” (which are often cut into smaller and more affordable half or quarter sheets for resale by our distributors).
Some types are not regularly offered any more, such as Green and Red Ab. “Heart” material, because commercially available shells have become so young and small that they haven’t had a chance to develop very much of the darker colors, or the central muscle-scar area from which heart is taken. This is also why farmed abalone, although useable, isn’t being processed, as they’re even more pale and colorless than the smaller (minimum legal sized) “wild-caught” animals.
Most abalone species suitably large enough for making inlay materials are generally not threatened, listed, or endangered, other than one or two species such as the Black Ab. (Haliotis cracherodii) and the Red Ab. (H. rufescens). We do have a small overseas supply of old pre-ban and some legal Mexican Red Ab., but not enough to make it generally available. The beautiful bluish New Zealand Paua Ab. (Haliotis iris) fishery has for many years been monitored and tightly controlled by that government, so although catch is closely monitored and limited, the animals are not in any danger. The Green Ab. (H. fulgens) and Pink Ab. (H. corrugata) fisheries in Baja have also long been closely managed and overseen by the Mexican government in solid cooperation with local fishery villages who practice strict regulatory self-enforcement in order to preserve their historical income sources. We foresee no shortage of real shell for guitar ornament, although smaller shells mean increasing use of pale, and less use of dark, colors (unless we’re successful in finding a way to penetrate full-thickness shell material with artificial dyes!).
Shell usage in and of itself puts virtually no strain on any of the fishery resources, as shell is but a byproduct along with guts and trimmings (waste, or “offal”) of the lucrative food meat industry for which the fisheries and farms exist, and raw shell value alone is so small that it wouldn’t be profitable to fish or poach animals for only that reason. Commercial taking of the large California Red Abalone has been shut down, and there are now serious seasonal closures and limit restrictions on sport dive limits as well, due to several factors: depredation by sea otters (which are a protected species) who prefer not to eat much of the animal other than its gonads, decimation of the North Coast populations by the still mysterious “withering foot disease” which first endangered the Black Abalones several years ago, deadly algal "red tide" kill-offs of breeding populations, severe storm damage in shallower waters, and a natural cyclical (every 20 years or so) El Nino coastal current change from nutrient-rich cold water to nutrient-poor warm water.
Even though shell is sometimes used in the manufacturing of cutlery, furniture, jewelry, fishing lures, “reverse glass” signage, billiard cues and tables, custom automotive graphics, and more, these are all very tiny and insignificant uses compared to the volume consumed by the guitar market. We process between 100-300 metric tons of shell per year, and probably 99% of that is for instruments. Laminated Abalam® shell sheets offer several ecological (as well as manufacturing and artistic) advantages:
1) We get 400-600% more material out of a shell than if it was processed into old-style solid flat blanks, thus easing pressure on and extending the life of precious natural shell resources.
2) Since once-unusable small-sized or thin shells can now be made into Abalam®, commercial pressure is spread over a much greater range of species than formerly, and shells which were once discarded as almost pure waste are now being utilized.
3) When cutting inlay from large sheets, the parts can be very tightly nested together, greatly reducing the amount of unused waste which was so typical of the old-style but much tinier “solid” blanks.
4) Since production is so much more labor-intensive than with solid pieces, significant jobs and income have been produced for some very destitute but highly skilled people in South Korea, Indonesia, Vietnam, and the Philippines, where our supply partners are located (we pay well over the local rates, and employ two cripples in making round dots – no so-called “Nike” kids!).
Non-environmental factors:
One ongoing problem in the supply chain is more economic than environmental. Ever since early 2003 China has been attempting to completely buy out every shell from every fishery in the world, through what appears to be a subsidized bankroll to a South Korean businessman. From what it looks like, the abalone contracts in all Mexican fishery co-ops (both private and government-operated) are involved in the equivalent to Mexican and/or Chinese “Mafia” control. That makes it increasingly risky to directly and personally deal with Green and Pink abalone sources. Shells can still be procured (at least in smaller amounts) but the grading system has changed since the old days, and “top grade” shell now contains a lot of sub-grade material, with little chance of being able to re-negotiate either the grading or the pricing. Even if one were to personally regrade shell at the fishery, what would actually be shipped would be something else, since the commercial system in Baja isn't free of corruption (even though much improved over what it was a few years ago, and the fishing grounds themselves are excellently managed).
This seemingly unlimited funding by China, who is always willing to pay more than you are, has driven worldwide raw shell prices up more than 600% in the last decade. Producing traditional solid blanks will waste anywhere from 85-95% of shell by weight. In comparison, although much more laborious to make, veneer and Abalam® sheets yield vastly more usable material, extending the life of these natural resources while spreading commercial pressure from 4 or 5 species to around 18 or so (and finding use for shells which formerly held little utilitarian value because they were too small or thin for making solid blanks of workable size).
Solid shell blanks remain limitedly available, but they’re understandably expensive and ultimately waste much material that could otherwise be saved and put to equal use. Even so, solid shell still retains an aesthetic advantage over Abalam® for some specialized applications.
What is the market impact of laminated Abalam® shell being used on cheaper instruments? How does the availability of your laminated shell affect luthiers' decisions of how to ornament what they build? It seems to me that there was a huge increase in abalone rosettes on pretty modest guitars at some point in time.
The introduction of Abalam® did seem to stimulate increased shell usage, but this coincided with mushrooming market conditions which were already in motion regardless of the newer shell becoming available at that time. Many more instruments from many more sources opportunistically took advantage of better and cheaper shell, but the guitars would have been built anyway with or without shell trim as an option. Top end guitars would still have featured inlays using existing shell materials, so it’s not so much an issue of whether these would have been built but that the new shell products influenced how they could now be ornamented. The greatly expanded choices introduced by Abalam® (as well as reconstituted stone and other non-shell materials) gave hand inlay artists a much broader range of expressive design techniques, while also creating a perfect fit with the new CNC production capabilities in larger factories.
Being able to trim a cheaper instrument in shell gave it the appearance of what had traditionally been much more expensive models, and this actually worried us quite a bit – would this cause manufacturers to avoid using shell trim because their high-dollar guitars would now look like many of the more modest ones? It turned out to be a non-issue because:
1) To not use shell really would visually downgrade the instrument, and expensive guitars wouldn’t look as good as the cheaper ones!
2) Although many retail dealers (like Frank Ford at Gryphon, in Palo Alto, CA) complained about getting tired of (and even irritated) seeing shell on everything from every manufacturer, the players loved it and kept buying everything at all price levels.
3) Shell has enjoyed a centuries-old tradition of popularity as instrument trim, not based so much on fads or marketing factors but just because it’s the only material available that can intrinsically produce such shifting and brilliant color changes, catch the eye at great distances, and become more noticeable in dim-light conditions (it actually “gathers” and intensifies available light, as in darkened indoor club venues).
Is it cheaper to use solid or laminated shell for guitar inlays, and if laminates are cheaper for factories to use, shouldn't they pass the savings on to the customer?
This is really a not-so-simple question: As an example, shell installation time for an experienced luthier on a top and sound hole rosette took about 1 1/2 - 2 hours using the older solid shell strips, which is now down to 5 - 15 minutes with CNC-cut Abalam®. Material cost (not current values) for solid shell would run $42.25 (Green Ab.), in Abalam® $68.75 (for Green Ab. "Light"). If doing traditional Martin style D-45 body and neck trim strips, materials would be: solid $136.85, Abalam® $239.75.
So, since the materials cost is quite a bit more using laminates, does the savings in installation time make up for that? That depends on how busy a shop is (if not busy, they make more on a job doing it the old time intensive way), and what a builder figures his labor time is worth (the more it's worth, the better the laminates look!).
But a factory parses things out a bit differently than a one-man shop. They aren't so much concerned with how much they save in paid-out labor, as they are with how many "units" are produced in an hour. If they're paying a worker $10.00/hr. to install shell for 1.5 hrs., then a top and rosette using "solid" strips would cost them a total of $57.25. The same worker using Abalam® and 5 min. time to put it in would cost in total $69.58/top. A factory also amortizes all kinds of other overhead into the equation per hour, such as utilities, insurance, advertising costs, etc., bumping it up even more. But, if the factory gets, say, $300.00 for each shell top/rosette, then using Abalam® the production goes from 1 top/1.5 hours to 18 tops/1.5 hrs., which in dollars is $300 worth of tops as opposed to $5,400 for the same time span! If we subtract costs of materials and labor, profit for 1.5 hours of factory time goes from $242.75 up to $4,147.56, even though the cost/top is greater.
Is this fair, or should this be passed on to the consumer? Most operations in building an instrument are only marginally profitable, for small as well as large makers, but inlay is the one area where a builder can finally make a very decent return! From a builder's perspective, if the market is comfortable with a certain price for an instrument, why not keep the pricing the same while simultaneously not sacrificing quality, improving your cost basis, and making more profits on the same item? Where is this ripping anybody off? In fact, what we now see is a new advantage for guitarists, who can for the first time find playable $300.00 instruments with shell trim and inlay, a proof that shell laminates really have made nice looking instruments more affordable. Some factories have passed along certain advantages after all!
METHODS OF WORKING SHELL
Shells and Mother of Pearl – Knowledge Base
How is inlay done?
What's covered here is only a basic primer, but along with lots of internet advice (not all of it equally good!) there are excellent books and DVD's available by the best in the field. These will hurt you in the wallet but are a necessary, not optional, tuition for anyone seriously committed to becoming an inlay pro in the shortest length of time:
"THE ART OF INLAY", by Larry Robinson, well-known master of materials and inlayist to the stars! Text covers basics as well as the latest high-tech methods and tricks, bringing us all up to speed in any easy to read format. Lots and lots of color, many other top artists are featured and their secrets exposed. Includes a 7 page chapter by the Dukester on "The Colorful History of Inlay"!
"PEARL INLAY", by James Patterson. A classic manual, softbound, 82 pages, lots of black & white photos and drawings. Much less modern than Robinson's book, but has more detail about dealing with raw shell, making your own blanks and strips, doing inlay repairs, etc.
"A GUITAR MAKER'S CANVAS", by Grit Laskin. Not a how-to book, but a large-format full-color presentation of some of the world's best inlay that's indispensable for design inspiration.
"GRAND COMPLICATIONS", by Grit Laskin. Another full-color coffee table book, but this one dives into the thinking processes, design evolution, materials choices, and back stories on 50 inlay works of art.
"THE INVISIBLE LINE", by Larry Robinson. A full-color book that presents Larry and 6 other elite west coast luthiers and craftsmen discussing the philosophy behind their work, and the hard to define distinction between craft and art. Great inlay is as much about the way you think as the way you work.
DVD "BASIC INLAY TECHNIQUES WITH LARRY ROBINSON". If you enjoy fine handwork, but have never handled a jeweler's saw, this video will walk you through the making of a nice little butterfly inlay, using several types of shell. Good details, close-up shots, no skipped steps, a discussion of mistakes to avoid, and a bit of humor make this a disarming and pleasant experience. 2 ½ hours.
DVD "INTERMEDIATE INLAY TECHNIQUES WITH LARRY ROBINSON". Intended for those who already have some experience using a saw or watching other videos, Larry shows in detail the progression of a fancy guitar fingerboard vine from the customer's rough sketch through final engraving. Nothing is left out in this 2 ½+ hours presentation.
DVD "ADVANCED INLAY TECHNIQUES WITH LARRY ROBINSON". Methods far past top-dead-center for all you compulsive overachievers who like to exist on the hairy edge of free-style inlay! Signatures, lettering, curved-surface work, and 3-D inlay tricks for a bit more than 2 hours of adrenaline-soaked thrills. Steroids optional.
Laying out patterns on the shell:
Along with drawing the patterns oversized and then reducing to get finer lines, it's important to use the correct type of adhesive when gluing the paper patterns to the shell (or whatever material is being used). If the glue is soft or rubbery it will interfere with your fine control of the blade by balling up in the teeth instead of clearing away as you cut. So, avoid rubber cements or aliphatic glues – the fastest curing, bonds to everything, easiest to handle, and most hard-drying (and best smelling) is Duco Household Cement (in a toothpaste-type tube). Just put a dab on the shell, smear it around quickly with a fingertip, and very quickly slap the pattern down on it before it dries. Smooth the paper out and expel any bubbles or excess glue by pressing or rolling the paper with a fingertip, but be careful as the wet glue may smear an inked line. If you've been using other glues, this should make a noticeable difference in ease of cutting!
Leave the paper pattern on the inlay right through to gluing it in the cavity, because if an inlay breaks it will keep the pieces perfectly aligned and repairable/usable (but this only works with darker, grainier shell like abalone, not with white MOP).
Blades and lubricants:
One thing that really makes jewelers saw blades last longer (as well as lubricating the saw cut) is to use a beeswax-based dressing called BurLife® Stick Lubricant, available from Rio Grande Jewelers Supply: www.riogrande.com, or (800) 545-6566. Instead of stopping to apply the BurLife® lube on your blade, just quickly wipe it over or across the lines on your pattern before you start so the blade will continually be lubricating itself as you cut.
Rio Grande also is the source for Laser Gold™ blades, the choice of almost all full time inlay professionals since the blades are extremely tough, break-resistant, and long lasting.
Blade tensioning and shaky or uneven cut lines:
When sawing a shape, the biggest factor in keeping a blade on the line is having it as taut as possible, as any slackness at all keeps it from responding to changes in direction – it should be just a breath away from snapping if tightened any further!
If it’s hard to keep the blade from wandering it's almost always due to the blade not being tensioned tightly enough, a very common problem with inlayists who often don't know how to solve it, since it's a real balancing act between either under-tightening or breaking blades from overdoing it (especially with the smaller blades such as 8-0's)!
Extremely delicate tensioning is almost impossible to gauge correctly when the method involves having to use body-weight while compressing the saw frame against a table edge. Because of this problem, I early on switched from the newer X-Acto style saw frames to the much older Swiss or German tools which had the extra wing-nut at the end opposite the handle (and often a sliding, adjustable, lockable frame). This is why I always have a few of these very old saws for sale on our table at the shows, as they're fairly difficult to find any more, even on eBay, and I always sell one or two at every event to artists that are catching on to the trick. The sliding frame allows use of different sized blade segments, but the most critical advantage is the extra tensioning nut: for any given blade size (or brand) I would mount a blade in the frame with the adjuster fully extended toward the blade, clamp down both ends, and then take up any slack by tightening the end nut. Once slack has been removed, give the end wing-nut half-turns, counting each one, until the blade snaps. Do this with several blades to get an average count on the half-turns; when ready to cut, mount a new blade by stopping one or two half-turns shy of the breaking point and you'll find it stays on track amazingly well! For various blade sizes/brands make a note on each package or storage container of the half-turns required for that particular blade.
If the blade is soft and has too much play, correct tensioning will definitely make a huge and immediate improvement in feel and control: if a blade's not tight enough, it won't quickly respond to changes in direction but wants to stay on the same track. Never consciously worry about gaining speed, which will naturally come on its own (as in playing an instrument), but instead focus on accuracy and control. When doing curves, short fast strokes work best (the tighter the curve, the shorter the stroke) while on long straight sections a slow full stroke keeps things on the line. Swimming marine animals especially usually have very smooth, sleek surfaces and outlines, so getting rid of any roughness in the cut would be a real advantage in your choice of subjects!
A line that's too fat is difficult to follow, since the blade can go in and out of the edge of it (without crossing all the way through it) without a nearby reference point for the eye to correct against. A good way to get finer lines is to do the artwork at actual size (unless you're comfortable working bigger), enlarge it to maybe 2X, retrace it using a fine point pen, and on reducing it down again your lines will be super-fine and any shakiness in the larger drawing will just disappear. With a line like this you can actually learn to cut very precisely to either the inside or outside of its width – especially useful when using the same drawing for laying out the cavity as well as the inlay without scribing (as when sometimes doing complex inlays of shell-into-shell).
It'll be a lot easier to control the width or taper of engraved joints between pieces if the suture or junction itself is even to begin with, as the graver's point will always tend to mimic any large irregularities it encounters. It also helps to selectively "prep" narrower sections of the line with a graver, so it's at least of uniform size along its full length, before actually engraving the full line to final width.
Transferring the shape to the substrate:
I use several methods, depending on how fragile the pieces are. For most inlays I use a metal scribe with the point filed straight (untapered) and narrow, but have also used a heavy sewing needle in a wooden handle (one that's too small flexes and requires more pressure than I care for). A carefully scribed line stays exactly next to the inlay, whereas a pencil follows the exact edge only when it's perfectly sharp, a condition that doesn't last very long at all even with a hard lead. After removing the inlay, rub away any loose burring from the scribed line and then just route to its inside edge; for better visibility, you can quickly run the sharp point of a white or silver art pencil along the scribed groove, which highlights both the inside and outside edge of the line making it easy to cut to the inside, the center, or the outside of your mark.
A word about gluing inlay down preparatory to scribing: for normal small inlays, I use two or preferably three tiny dots of Duco household cement on the back of the piece, correspondingly located according to marks previously penciled on the face (so I'll know where to razor the glue loose later). It dries fast, smells good, and gets hard so the inlay won't shift from the pressure of scribing up against it (unlike rubber cements, double-stick, or contact adhesives). Carefully sliding a razor edge under a piece usually releases it, and any glue remaining on the backside can be easily shaved off. On very delicate shapes, a drop or two of acetone next to the inlay quickly wicks underneath and loosens things.
With extremely fine or fragile pieces, I'll sometimes position them exactly without gluing them down, and then mask off as much open space around them as closely as possible using Scotch or masking tape. Next, I gently sift talcum powder over them while very softly blowing with my mouth to make sure the powder gets into all the little nooks and crannies of the outline (just don't blow so hard that you move the shape!) – dipping a toothbrush in talc and rubbing it on a small piece of fine metal window screen held above the inlay creates the right effect, and the talc should be in a very sparse layer with the wood still mostly visible, not thick or piled up. Then carefully peel up your pieces of masking tape without spilling any excess powder on the surface, and use a tweezers to lift the inlays straight up without disturbing the powder around them. Lastly, lay thin clear cellophane tape over the surface, trapping and stabilizing the talc outlines to which you can then route. It's kind of tricky, but I've done some impossible stuff using this funky method!
I haven't tried this, but it might work to just lightly mist the inlays using a can of white spray paint, which would eliminate a lot of hassles, and any paint could be removed from the pieces by rinsing or soaking in an appropriate solvent.
Bits and routing the cavity:
I always did all my inlay freehand, which offers some subtle advantages over platform routing but does require a lot more fine hand control. Dremel is notoriously sloppy in the quality control on their bits, but sorting through a rack of them usually produces a few that are close to being round or sharply pointed! Dental bits are great, and after being used only once by a dentist are just tossed, although still plenty sharp for inlay work. They cost nothing if recycled from your own doctor, who probably won't mind also sterilizing them for you.
Use a #118 Dremel bit (or any similarly pointed cone shaped bit) for fully outlining the cavity, holding the Dremel or Foredom handpiece at an angle so that one side of the cone cuts a vertical wall up to the scribed line around the inside of the cavity; for cutting into sharply-pointed inside shapes (such as the tip of a leaf), just lay the bit almost horizontally into the point and then raise the handpiece more vertically as you draw the bit towards you into the wider part of the pattern. This will leave an "island" of wood in the center of the shape which can be hand or platform routed using regular small end mills. Most luthiers supply houses carry left-hand spiral end mill bits which will minimize raising burrs or chips around the edge of the cuts, as they cut downwards instead of upwards.
A little strip of masking tape around the bit just above the cutter head, with the two ends joined to form a small "flag" sticking out from the shank, makes an effective "fan" that blows dust away as you work.
Fillers and gluing the inlays into the cavity:
Using sawdust with white or aliphatic glues, or superglues, can cause problems:
1) The sawdust filler dries darker than the wood's natural color.
2) If the inlay is (hopefully!) a close tight fit, the gritty sawdust can keep hanging up the inlay as you try to seat it in the cavity.
Water-based adhesives, or epoxies which have water-attracting nylon fillers, will remain sensitive to changes in humidity and cause the filler around an inlay to swell up in damp conditions and shrink in dry times. If you then sand things flush when the filler raises up, it'll later sink below the surface when it dries. The solution is to use epoxy systems that don't contain nylon "bulking agents", and instead of sawdust use proper dyes made for resins.
With woods that contain varicolored grain, such as rosewood, make several small batches of epoxy each tinted to one of the colors in the wood, then fill each inlay cavity using multiple blobs, at least one of each color, which will produce a variegated color line around the inlay that's much more difficult to spot than a solid dark color line.
Lastly, push the inlay down once into its glue-filled cavity, and then resist the temptation to "seat" it by wiggling and rocking it, which will only produce gaps and bubbles around it that will need to be touched up later.
If a cavity is cut too deep for the thickness of the inlay or if you're trying to preserve the surface color or figure of a piece of shell by keeping sanding to a minimum, simply superglue a couple of pieces of flat toothpick across the top of the piece, letting them overhang to each side, and the inlay will sink down even with the surface but no further. If using epoxy rather than superglue as filler, lay very light weight on top to keep the inlay from "floating" back up while the glue cures.
This trick works best if you first shave off any paper pattern and glue the toothpicks directly to the inlay itself. Otherwise, the inlays will be sitting a paper thickness below the surface and require sanding to bring the surrounding surface down to their level. When not using the toothpick technique I almost always leave the paper patterns attached the entire time, especially with abalone shapes, because if a piece breaks cleanly while being handled or scribed the paper acts as a hinge which keeps the pieces in register with each other while being superglued back together. You can get away with this in materials which are dark and/or patterned enough to hide a crack line, but M.O.P. or pale colored pieces can't be salvaged and need to be re-cut.
I am a laser tech by trade, and have discussed laser cutting shell materials with other people in the industry. It seems that the CO2 laser cuts Abalam® shell laminate well but does not work as well with thicker raw shell. I am going to cut using high power green laser or ultraviolet laser, as I have both. I have come across a zero-heat laser process that may work, but again the speed of cut will render it useless for manufacturing. The green laser seems to do the least damage so far. Do you have any advice? Has your company done trials with these types of laser? I will undercut my inlay cavity on the guitar I am building so the burnt edge in the wood will not be visible.
We experimented with laser cutting of solid shell back in the early 1970’s and again more recently in 2005-2006 with minimal success. This was with either laser manufacturers or laser service businesses, not just retailers or “kit” type manufacturers custom-assembling parts supplied by other companies, and included three companies who made industrial high power and CO2 units, and who were dead certain their machines would succeed. I’m certainly not at all knowledgeable about fine points of laser technology as such, but so far no one we’ve worked with has been able to come close to the clean cuts produced by high-speed rotary tools, contrary to results promised by these laser pros!
Along with more power and different laser elements, one of the things they were playing around with were various and novel systems of lensing/focusing, but they eventually just gave up on the “sure-fire” ideas they had been so positive would work. Sort of disappointing, but the type and strength of the laser don’t seem to affect results, assuming things aren’t just underpowered to start with. Aqua Blue Maui [use live link from "Industry Sources"] uses laser for fabricating some paper-thin inlays or overlays used in ukuleles, small boxes, wood-barreled writing pens, etc., but their stuff always looks slightly rough and cheap (at least partially because they also laser the cavities and there’s always a slight burn around the edge in the wood, making it look sloppier than it really is). Michael Gurian [use live link from "Industry Sources"] has by far the most experience with industrial laser cutting of shell, but limits that to material under .015”.
It’s true that the veneers and also the laminated Abalam® sheets both cut fairly well. A thickness of .015” seems to be the limit for laser-cutting single layer shell (not laminated, and of course too thin for most inlay work which usually requires .030"-.080" material). Anything thicker than that starts to show visible degradation of the cut, such as roughness, burning, chalkiness, crumbling, etc., and the thicker the material the worse it cuts. In this very thin shell, the damage is still present but isn’t noticeable to the unaided eye. In the multi-layered Abalam® material, the individual layers are usually around .008”-.010” thick, so damage for each layer is automatically limited, probably buffered somewhat by the epoxy between shell layers which perhaps acts as a natural insulator or heat-sink so that excess heat doesn’t build up.
My personal theory about the difficulty is that since shell contains about 1-4% water at a molecular level locked into the scleroprotein matrix, as soon as a laser hits this moisture it explodes out of the side-wall of the cut, taking microscopic bits of brittle nacre with it and creating the uneven, crumbly look. A stronger laser may speed up the cutting process but it also just speeds up the damage created. It wouldn’t seem as though first cooling the shell would accomplish anything, since in order to produce a cut the cutting path still needs to get up to the same temperature anyway in order for the shell to vaporize.
As for undercutting when laser cutting the inlay cavity, that may work on a one-off hand-made instrument where an individual luthier is able to finely control tolerances at every point of construction; but it wouldn’t be acceptable in a production situation where quite a lot of material is often dressed off in the final leveling steps, which would progressively reveal more and more of the undercut around the inlay’s edges.
The high-speed overhead rotary systems have become quite inlay-specific and sophisticated, and are going to be hard to even match, much less improve on!
Like the sand blasting and abrasive water-jet technologies we’ve also investigated, laser systems will need to offer much more than just equality with, or small advantages over, the very expensive, familiar, and time-proven rotary equipment now being used so effectively. Start-up companies might spring for a new technology if they’re not yet invested in the current systems, but everyone with existing and fully-tooled operations would need to be strongly convinced that laser offers substantial financial or quality-control advantages before they’d be willing to switch to something new. It could of course happen, and may even be inevitable, but there’ll be a lot of resistance (unless costs and/or efficiency are sufficiently attractive)!
Can shell be cut using sand blasting, or a water-jet?
Sandblasting works best in thinner shell, but in thicker shell the sand begins to scatter after initially hitting the top surface which results in a rough and tapered undercut instead of flat, straight sides.
Shell veneers:
Paper-thin shell is new to the U.S. but has been used for centuries in the Orient. This amazing material is quickly finding important uses in a number of industries where inlay as such would be impractical, larger areas need to be covered, or costs lowered without compromising existing quality. Traditionally referred to as “feathers” in the 1800's, these materials are very thinly sawn single pieces of shell about .006”-.013” thick (we can supply as thin as .004”), which are moderately flexible and often transparent enough to allow very effective use of various materials directly beneath them. 5½” x 9½” veneer sheets are made from multiple smaller veneer pieces. Often these various veneers will display their deepest colors if placed over a black substrate, but overall tone can be greatly influenced by the use of colored backgrounds, painting color on the backside, or sizing and leafing the reverse with gold, silver, aluminum, Dutch metal, copper, or even thicker foil materials. Not really thick enough to use as an inlay material, veneers are intended for “overlay” work and are so thin that lacquer or enamel finishes can be built up flush with the shell and then buffed down level.
Uses include covering or capping banjo pots and resonators, as well as applications on pegheads, heel caps, truss-rod cover plates, furniture, fishing lures, box tops and sides, nameplates, picture frames, and many other items. “Artistic” sign makers and automotive pinstripers often use feather veneers in combination with gold leaf and other techniques to fill or outline ornate lettering or designs, often behind glass (“reverse glass” work). Shell decals are also a possibility! To cover plastic tuning knobs on stringed instruments, the shell is super-glued to both faces of the knob, the edges dressed off, and the knob’s perimeter wrapped with shell and dressed off. To keep veneer from breaking apart while being forced onto a curved shape, it helps to first cover one side of the feather with heavy clear packaging tape, which is then removed once the shell is glued down. This is a trick developed by the Custom Shop at Fender Musical Instruments, and is how the knobs are made as sold by Harvey Leach [use live link from "Industry Sources"].
Trimming can be done on simple shapes using a razor or even a sharp scissors; or veneers can be temporarily bonded to a thin backing material, cut with a saw, and then released by soaking in water or other solvent. For producing intricate shapes, several methods have been used: computer (CNC) cutting of glued-down veneers; cutting a glued stack of veneers that are later separated; or masking and then sandblasting.
Sandblasting:
For sandblasting, the veneer is glued to a piece of scrap window glass (available free at any glass shop) using “textile table adhesive” (available through a sign maker’s supplier), covered with vinyl mask (“frisket paper”, also a sign shop material), the pattern being drawn or transferred onto the frisket, and the frisket cut along the pattern lines with a knife or razor (or computer-cut frisket patterns can be used). The background paper is then removed (“weeded out”), and the shell blasted with a very fine sand until glass is reached. Use a citrus based glue or label remover to release the veneer from the glass, then soak about one hour in water to remove the frisket from the shell.
Veneers can also be painted or silkscreened with a design that leaves exposed the areas to be seen as shell, then protected with a clear finish. We can supply further advice or sources on any of these methods.
Water jet:
Cutting shell inlays with water jet technology has been discussed/considered many times. It will cut shell, as I've had a few cuts made in local shops, but don't know anyone who's seriously tried it, mainly because:
1) Working with the wet abrasive slurry is messier, and introduces different problems, than when working dry.
2) It would take big bucks to set up (or re-tool) just to get an unproven system.
3) Having evolved through several generations, overhead rotary cutting systems are now highly sophisticated and efficient, and there's no guarantee that water jet would produce any significant advantages.
Methods of Shell Strip Installation
On soft curves such as around a guitar body, straight pieces are placed over a glue-filled channel and then forced into it by breaking into smaller pieces, the more the better, to conform to the curve. The breaks will be all but invisible in most abalone, especially in “Dark”, "Select Color", or “Heart” grades; pale shell types are also used, but those with more internal “figure” such as Donkey Ab., Agoya, Korean Awabi Ab., or Green Ab. Rippled will have less obvious breaks. Some factories and even productive small shops are now having veneer ply material cut into huge curved sections which can fit an entire guitar top with only 9 or 10 segments, with virtually no need for breaking to fit! In the tighter curves of a waist or cutaway, some builders prefer starting with curved rosette material and breaking to fit.
When installing the classic Martin-style “D-45” type of guitar trim, luthiers have developed several approaches. The laminated shell handles differently than old-style solid shell strips, not requiring as much force to break and allowing more breaks per inch, which results in a smoother looking job around curved areas. Best results require installing strips using watery/thin super glue; but this method calls for any adjacent wood to first be sealed to prevent the grain from absorbing glue and causing staining/finishing problems. Taylor Guitars recommends brushing a light coat of clear finish into, and next to, the shell channel before installing the strips, which only takes a few seconds of effort and virtually no drying time.
Here are some of the methods being used to install the strips in their channel, but experience will quickly teach you your own approaches. Practice on scrap forms until you gain confidence and consistency.
- In a section of glue-filled channel, use the left hand to feed a length of strip into the groove, while breaking it to fit with the rounded back of a spoon nested under the right thumb (or the opposite for lefties). When shell is in place, flow thin super-glue on the surface to stabilize any chips.
- Same as above, either in a wet or dry channel, but the right hand mashes a strip into the slot by flexing down on a thin steel rule under the thumb, and sort of “trowels” the shell into position. Flood with super-glue before doing the next segment. This method leaves strips almost flush with the surface, greatly reducing the need to sand the shell down.
- In a dry channel, as above, but right hand uses a ¼” thick piece of clear plexiglass with the lower leading edge rounded off (sled runner fashion), which is pressed flat to the surface as it is moved forward and crushes shell beneath it. This method allows you to see what is going on as the shell is installed. As before, flood well with watery superglue to stabilize loose flakes before doing the next section.
- Left hand feeds long strips, right hand gently taps/breaks shell into its groove with a small mallet. Flood with super-glue to finish.